The Building Envelope: A Perspective
By Mark Stewart, RRC CEI, and Jeffrey Martin, RRC, RRO, CEI, REWO, CDT
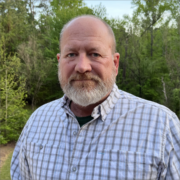
Mark Stewart
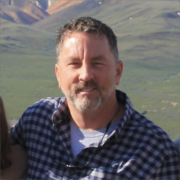
Jeffrey Martin
The construction industry has currently been running at a breakneck pace. This pace, combined with the advent of a pandemic, which brought us material shortages and delays, and a workforce shortage, put contractors in a tough spot to bring quality-built projects in on time and under budget. When the delays began, it forced contractors and designers to look for alternative material options that were more readily available. These new alternative materials, without intense scrutiny of their application, could affect the performance of the building envelope.
For example, in the case of wood-framed multi-family construction, the availability of polyisocyanurate (iso) rigid roof insulation was delayed due to shortages of raw materials. Iso was then replaced with a coverboard, and alternate insulation, such as fiberglass batt insulation, was used below the roof deck. This moved the dew point above the insulation, and thus, the interior moisture condensates on the underside of the membrane. The moisture then was at the deck level and began to saturate the wood deck. Over a short period of time, the deck fails prematurely and the increased levels of moisture in the attic space create the perfect environment for biological growth . . . mold. This is just one example of many instances of where the building envelope was compromised.
The material delays also affected the construction schedule, forcing the contractor to proceed with trades that could work ahead of trades that could not procure material in time. When this happens, subcontractors work against trades that should have been in front of the schedule, using details (if any) to complete their work and move on to the next project. This can lead to premature failure of the building envelope.
The depleted U.S. workforce in our industry and the current reliance on a foreign workforce, exacerbated by our current immigration policies, have forced many workers into the black market. What results is a workforce that is, in a lot of ways, separated from a traditional bona fide business. Usually, that trade contractor with in-house employees would be traditionally trained in the craft by older craftsmen within the business or outside (for example, material manufacturers) providing training. What happens is the black-market labor sub does not have that same connection to the training. Therefore, the workforce lacks the appropriate level of skillsets, and the quality of the work suffers.
The level of competence of many designers and general contractors overseeing these trades is lacking as well, so they are not catching a lot of deficiencies in the work being put in place.
We are in an era of construction in the U.S. that does not have belts and suspenders. The building envelope can be a complex system to keep the moisture out of the building and is often in jeopardy and has been getting contractors in hot water with litigation.
There are certain “guardrails” that can be put in place to mitigate poor construction and promote quality construction methods. They most certainly start with a good design and follow up with consistent scrutiny during construction. If all the designers and contractors would do those two things, it would make a big difference. Third-party oversight can help. It takes a large burden off both the designer and the contractor, and now, they aren’t “the bad guy,” and there can be more confidence to the owner that they are getting a quality installation. There has been an uptick in the number of third-party inspections, but we have over a decade of construction where it has not been very prevalent.
In construction, we have a rule. You can get it good, fast or cheap. You can only pick two. We can only hope that “good” is always one of the two. But hope is not a strategy!
This post has been sponsored by Fortress Building Envelope Consulting.
Mark Stewart has 33 years of experience in the commercial roofing and waterproofing industry. Working in estimating, project management and consulting, Mark has been a part of a wide variety of building envelope challenges.
Jeff Martin has 36 years of experience in the commercial roofing and waterproofing field. Working in both the contracting and consulting ends of the industry, Jeff has a broad experience in all areas of the building envelope.